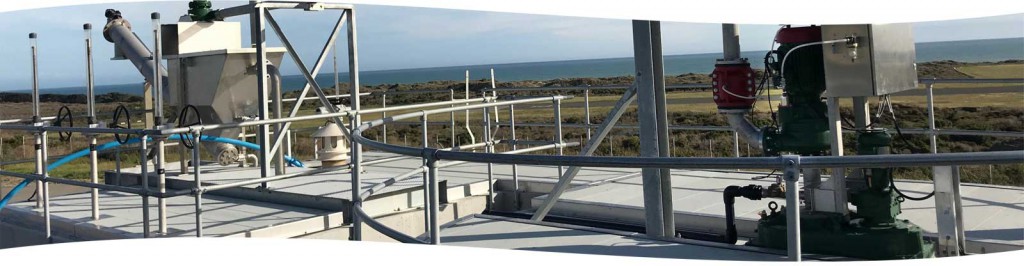

CST – as the authorised Australian representative of Smith & Loveless – can offer a range of S&L grit pumps and grit removal technologies, and provide local service and maintenance as required.
S&L’s PISTA® TURBO™ Grit Pump
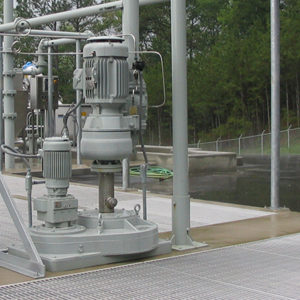
Smith & Loveless’ rugged PISTA® TURBO™ Grit Pump is the only pump in the industry exclusively designed for pumping grit separated from sewage. Available in both top-mounted vacuum-primed and remote-mounted flooded-suction configurations, the grit pump features the exclusive staples of S&L wastewater pump design: an oversized, stainless steel shaft and oversized bearings. The pump utilizes a single mechanical seal, which eliminates need for seal water filter system. Top-Mounted units eliminate expensive piping (and also aiding in reducing risk for plugging) while lowering the head and horsepower requirements. This combination yields reliable grit pumping and the velocity required for effective grit washing and dewatering devices. The pump is available in both 4” and 6” (100 and 150 mm) piping arrangements.
Features & Benefits
- Direct coupled design
- Ni-hard construction (nickel-based alloy) is more durable than cast iron
- Recessed impeller protects from direct flow path and reduces potential for plugging
- Long seal life
-
Remote-Mounted, Flooded Suction Grit Pump Oversized bearings and stainless steel shaft
- Heat dissipating bronze seal housing
- Maintenance is simplified and cleaner with the need to remove just 4 cap screws to access the pump volute and impeller.
- Top-mounted and remote-mounted models (offer design flexibility)
~ Top-mounted offers space-efficient benefits (utilizing vertical space) and lowering overall installation/construction costs.
~ Top-mounted allows for typically simpler grit path to dewatering components.
~ Flooded-suction types eliminate need for priming, therefore providing an even easier pump to maintain.
What About Self-Primers?
Self-primers have a lot of problems. From the potential to freeze & crack in cold weather, to less durable construction and more, here’s some info on self-primer pumps.
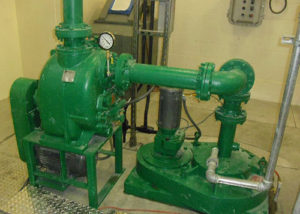
Horizontal orientation
~ Requires elbow in suction line (where grit can accumulate and plug).
~ Flow through impeller with wear plate can lead to grit plugging.
~ SP models contain a check valve where grit accumulates and causes vacuum leaks resulting in priming issues and abrasive wear.
More wearing and adjustable parts than S&L type
~ Belt driven, which requires adjustments and eventual replacement.
~ Contains wear plates (at 10/1000in. or 0.25 mm tolerance) which require replacement over time in order to maintain 250 gpm (15.8lps).
Harder and messier to disassemble and service
~ Pulling the pump with horizontal casing is labor-intensive, requires removal of several cap screws (at least 8).
~ Must account for unsafe and messy sewage spills when volute becomes exposed.
~ Freezing and grit buildup in the casing.
Historically cast iron construction, which is less durable than Ni-Hard
Airlifts Are Old Technology
For nearly a decade, Smith & Loveless used airlift pumps for its grit removal applications. But we quickly realized the many faults of this technology, so we developed the first pump designed specifically for grit removal in the early 1980s. Some of the faults of airlift pumps include:
- An airlift has limited pumping capacity, in terms of pressure and flow rate. If a plug in the pipe occurs, the pressure and flow is not sufficient to unclog the line on it’s own. Plugged lines require O&M personnel to remove pipes and elbows to remove clogs.
- To increase flow rate with an airlift, the airlift submergence has to be greater, which means the design will require a deeper grit hopper basin.
- Because the airlift lacks the pressure and flow, the design cannot include a grit concentrator (cyclone), thus the disposed grit has more organics in the dumpster (more odor). The grit concentrators’ function is to wash the organics off the grit, and that device is not available with the airlift. With an airlift, the dewatering screw conveyor is limited to having an air vent, to let the air off the grit slurry.
- Airlifts have a limited TDH capacity.
- The grit pump has the capability to pump at a higher flow rate than an airlift and will thus evacuate the grit hopper in a shorter amount of time. Typically the grit pump will operate 2 to 4 hours per day versus an airlift that will be required to operate for 5 to 10 hours per day. The airlift requires the grit classifier to also run longer since they must operate together.
- Grit pumps are more energy efficient than an airlift.
Horizontal Belt-Driven Pumps Are Not Equal
Below is a list of differences and similarities between the Smith & Loveless (S&L) grit pumps and the specified grit pumps. They both have been considered in the industry as acceptable alternates to each other and interchangeable. Sometimes our vertical pumps gets specified and we lose them to a horizontal type pumps, and vice versa. Differences and similarities below:
- S&L uses a vertical, direct coupled pump versus a belt driven horizontal pump. Operators like not having belts to maintain, and appreciate the vertical arrangement of the S&L design. Vertical pumps allow for grit slurries to remain inside the pump volute when having to access the impeller via removal of the rotating assembly. The horizontal grit pumps when split open, allows the grit slurry to spill over the working area.
- S&L grit pumps take less space than the horizontal.
- S&L grit pumps don’t require shaft sleeves to the carbons steel shaft, nor do they require wear plates. The S&L design is driven by a solid stainless steel shaft with a diameter of either 1 -7/8” or 2-1/8”.
- Both S&L and horizontal pumps are specified as “non-clogging, recessed impeller, torque-flow vortex type.” They both have suction and discharge flanges. They both have Ni-Hard impellers and Ni-Hard volutes per specifications.
- Vertical pump configuration allows flexibility of installing the grit pump in a flooded suction or top mounted vacuum primed arrangement.