Sometimes the first indication owners have that their wastewater plant screens need maintenance is when they are subjected to sudden heavy load. This is both the time that they are most needed, and also the time when the worst failures can occur if screens haven’t been properly maintained. Then, the problem becomes all too obvious.
Raw sewage, or untreated food waste, seeps through plant and neighbouring surroundings, including sensitive land and waterways, with potential production halts, OH&S cleanup risks, pointed questions and potentially serious environmental consequences for public and private entities.
By Michael Bambridge (M.E., Chemical Engineering),
Managing Director, CST Wastewater Solutions*
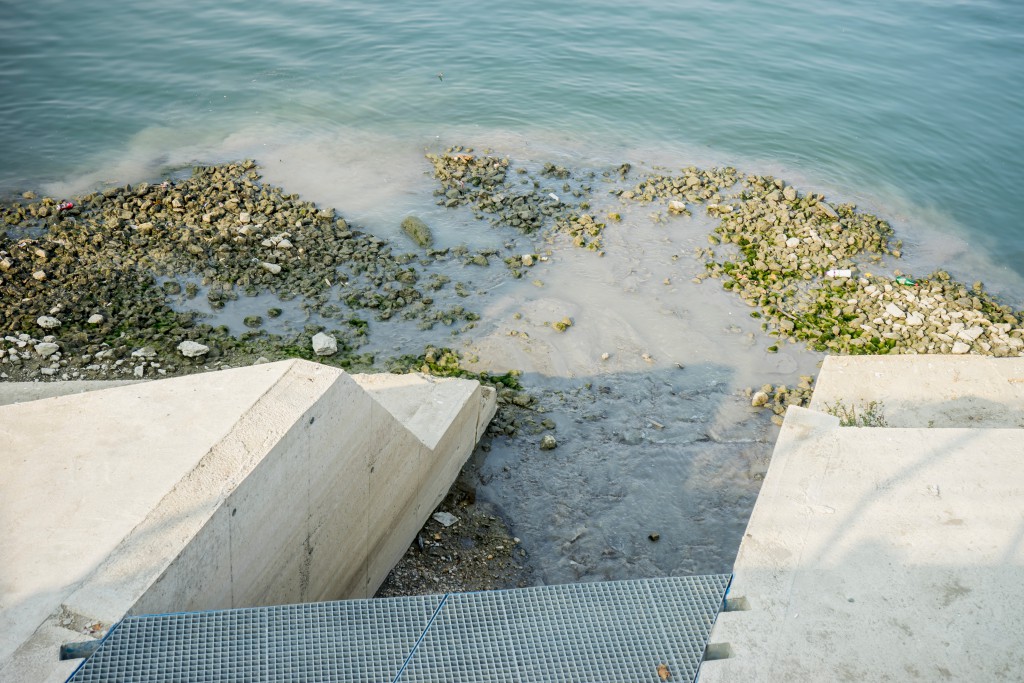
Sometimes the build-ups to these failures will extend over many years. Grit build-up over time in local authority WWTPs may not show up until sudden wet weather and floods. For industrial plants, the problem is often a result of excess solids or hydraulic loads – or it could just be simple mechanical failure somewhere in the process.
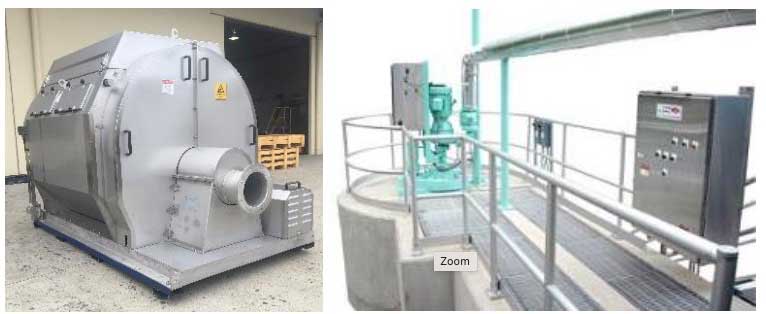
Screens are the first line of defence in a wastewater or waste management plant, so they get the dirtiest job of screening out all the lumps, chunks, strands, and unwanted foreign objects that can foul the often expensive, settling, clarification, treatment, filtration, and energy processes that follow downstream.
The inlet screens can look pretty good to the untrained eye, so the temptation may always be there to check and forget, to save a few dollars if there is no obvious problem. This set-and-forget approach can become a costly lesson for several reasons, including:
1. Screens do deteriorate over time. They may have a design life of many years in normal service – but regular routine service and maintenance is needed to keep them in peak operating condition. This can be particularly important in sandy areas (noting that municipal councils’ WWTPs serve more the 80 per cent of Australia’s population living within 50 km of the coast. Many industrial processing plants fall within the same heavily populated areas).
2. Screen technology does evolve over time. What was a fine mesh screen 10 or 15 years ago, may no longer be up to the job of protecting newer processes downstream. It could be a matter of upgrading the screen to a finer mesh type now available, or using newer technology (such as CST’s new horizontal rotary drum screen, which is specifically designed to protect downstream MBR (membrane bioreactor) plant.
3. Asset management. Inlet pre-treatment, including screens, is a robust but finite asset we all depend in the waste management business. The value of this asset should be maintained by regular servicing, just like a car. CST has some screens still operating after more than 25 years, because the companies involved have invested in cost-effective regular maintenance to extend product life and effectiveness.
4. Risk Management. Because screens are your front-line defence, they prevent or limit damage occurring in expensive processes downstream. These processes can be hard to get to if they do fail, then cause many more OH&S issues to rectify. Compounding the issue is the fact that many remote and smaller public and private waste treatment plants these days do not have the engineering manpower on hand to quickly rectify unexpected or complex and expensive events. We know how important the risk management is because we engineer dozens of waste management (and waste-to-energy) processes purpose-built to minimise maintenance..
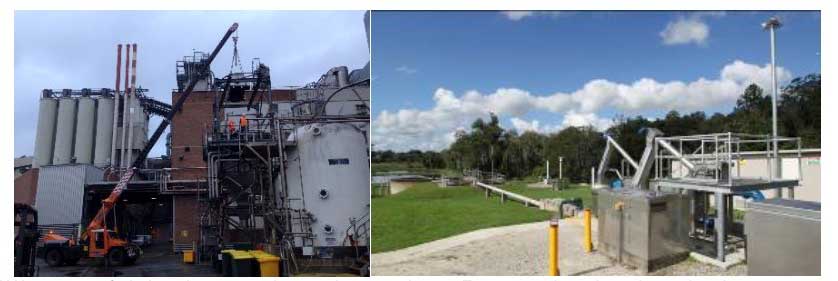
Most companies these days are pretty risk-aware. They know production stoppages are costly, and environmental spills can affect their statutory licence to operate.
But we still do see poorly maintained plants causing issues for the operator, reasonably often. These should be a thing of the past, when small investment in yearly maintenance and check-ups can return good value and ROI throughout the long term.
CST Screening and Grit Removal
Examples of CST’s screening and grit removal expertise include:
- Locally designed and built internally fed rotary drum screens and pre-MBR horizontal drum screens.
- Smith & Loveless, for which CST is exclusive local distributor, has invested significant research and development to provide a quantum leap in grit removal, with systems that can remove 95% of grit down to 105 microns, with 10:1 turndown. This is a major step up from existing grit removal systems that typically only remove grit down to 200-300 microns.
- The ability to retrofit a range of technologies, like those above, to upgrade the performance and operations of existing systems.
*Michael Bambridge is Managing Director of CST Wastewater Solutions. He is a Chemical Engineer with decades of experience in waste and wastewater management throughout Australia, New Zealand and South Asia, with particular expertise in local authority and food, beverage and agricultural production. In addition to project planning, execution and commissioning, CST Wastewater Solutions, has a dedicated full-time Services Division to the company, to complement its proven wastewater treatment, fine screening, and grit removal technologies. The company conducts annual audits of technology vital to cost- efficient, safe, and reliable processing.
The Services Division complements CST Wastewater Solutions’ engineer-and-build water and wastewater treatment and recycling packages, which are designed to lower the cost and complexity of such projects. The design, supply and install packages – incorporating global and locally manufactured technologies proven in use by some of Australia and New Zealand’s leading companies and councils – are aimed particularly at organisations seeking engineering assistance to develop clear choices and optimum solutions. The packages incorporate advanced low-maintenance technologies, which provide high levels of water purity while reducing maintenance, waste handling and OH&S issues associated with running them.